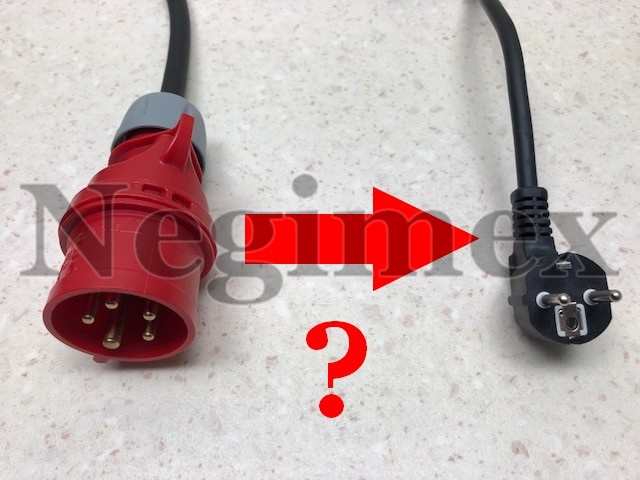
Il est, en pratique, possible d’alimenter un moteur de pompe de surface, initialement destiné à être alimenté en 400 volts triphasé, avec une tension de 230 volts monophasée. En prenant cependant en compte certains inconvénients, rédhibitoires (du moins, en ce qui nous concerne…). Si une installation fiable, destinée à durer dans le temps, est envisagée. Il faut en effet savoir qu’un changement de tension d’alimentation, réalisée via un condensateur permanent, peut s’avérer extrêmement aléatoire, et sera tout sauf une science exacte.
Si ce type de projet est envisagé, nous recommandons de protéger le moteur à l’aide d’un disjoncteur moteur finement calibré. Et cela afin d’éviter, dans le mesure du possible, la détérioration du bobinage moteur. Il faudra également impérativement effectuer plusieurs tests (fonctionnements courts), afin de vérifier la température et le rendement (cos FI) du moteur. Ce type de montage est à proscrire sur les motorisations dépassant 750 watts de puissance, du fait de la chute importante du couple de démarrage moteur et de la puissance délivrée en général. Les moteurs de pompe immergée ne peuvent pas supporter un tel montage, car ils nécessitent un couple minimal pour pouvoir mettre en rotation une partie hydraulique, et la maintenir une vitesse de rotation à environ 2900 tours par minute, tout en ne dépassant pas une certaine température interne.
Les inconvénients à prendre en compte si l’on alimente un moteur triphasé en monophasé
- Chute du couple moteur (30 % et plus), ce qui rend impossible la « transformation » des moteurs qui démarrent avec une charge importante.
- Le moteur aura tendance à chauffer plus qu’à la normale.
- Du fait de la chute du couple moteur et de la surchauffe, baisse importante du rendement moteur, et du ratio consommation électrique/rendement.
- Une perte totale de la garantie sur le moteur en cas de problème.
Les règles de calcul
- Diviser la puissance nominale en watts du moteur de pompe par 736, ce qui permet d’obtenir sa puissance en cheval. Par exemple, pour un moteur de 370 watts de puissance, l’on obtiendra (370/736) = 0,5 cheval.
- Multiplier la puissance en cheval obtenue dans le résultat ci-dessus par 50. Par exemple, pour un moteur de 0,5 cheval, l’on obtiendra (0,5 X 50) = 25. Cette valeur correspond à la capacité du condensateur à utiliser pour réaliser le montage. Préférer une valeur de condensateur standardisée arrondie.
Un boitier de démarrage, branché sur un disjoncteur moteur précisément calibré, peut être utilisé pour le montage du condensateur.
Ci-dessous, à titre aussi informatif qu’expérimental, les condensateurs et protections thermiques à envisager, en fonction de la puissance du moteur. Ces valeurs sont approximatives et sans garantie. Elles sont uniquement destinées aux moteurs de pompes de surface.
- Pour un moteur de 250 watts : condensateur de 18 uF – Protection thermique à partir de 1,30 ampères.
- pour un moteur de 370 watts : condensateur de 25 uF – Protection thermique à partir de 1,80 ampères.
- Pour un moteur de 550 watts : condensateur de 40 uF – protection thermique à partir de 2,40 ampères.
- Pour un moteur de 750 watts : condensateur de 50 uF – Protection thermique à partir de 3,00 ampères.